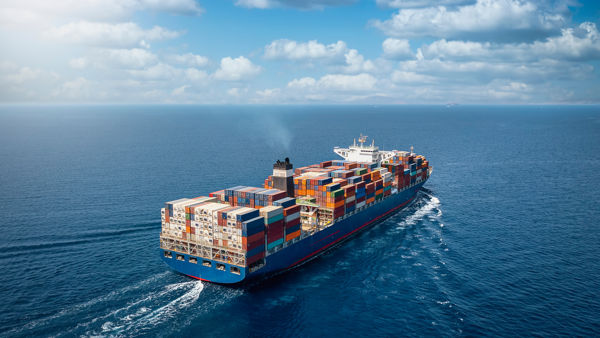
Hyperconnected ‘digital’ supply chains – A disruption or a competitive weapon for manufacturers?
Why UK manufacturers must place their supply chains under the microscope
The UK’s manufacturing industry came under siege at the start of the pandemic and has enjoyed little respite since. Whilst the UK and the rest of the world opened markets back up to trade, few predicted that global demand would exceed supply. Supply chain disruption is not only about the pandemic – it is also about cybersecurity, (the last few years have seen manufacturing overtake financial services as the most cyber attacked industry), severe weather caused by climate change, global shipping constraints caused by chronic labour and skills shortages, conflict in Eastern Europe, and rising inflation costs.
Differing scales of disruption and complexity over a prolonged period have exposed many “cracks” across the breadth of operational processes and revealed a disturbing lack of resiliency in many key areas of the supply chain.
Supply chain management has clearly appeared as a critical function for companies to realise their business aspirations, and supply chain resilience is fast becoming a highly competitive weapon in the modern digital economy.
A Robust Supply Chain
Assessing the robustness of supply chains has never been more important for the manufacturing industry. Over the last two years, there has been a spotlight on their fragility with recent data suggesting that 6-10% of annual revenue can be lost from supply chain disruption.
Today, customers expect you to have a strong and efficient supply chain. It is becoming more important from a regulatory point of view as well, with the UK’s modern slavery act as well as the forthcoming EU (European Union) legislation forcing companies to act.
Supply Chain Due Diligence
Supply chain due diligence is the ongoing, responsible management of your supply chain, based on the identification and management of ESG principles, (Environmental, Social, and Governance). Being accountable for your supply chain is now considered to be a core requirement for manufacturers.
Areas that manufacturers are exploring are:
- The complexity of their supply chains
- The distance from disruption
- The possibility of increasing their stocking levels
- Shortening their supply chains
- Reshoring & nearshoring
According to research by Make UK, 40% of manufacturers said they have increased their supply from the UK. A similar number said they will do so in the near future. There is, for sure, unrelenting pressure on company supply chains from increased costs and geo-political uncertainty.
Reshoring is the process of returning the production and manufacturing of goods back to the company’s original country, also known as onshoring, inshoring or backshoring. This can help strengthen supply chains as companies no longer have to deal with customs enforcement agencies and the complexities behind international logistics. In the wake of Brexit, UK business es are desperate for simple, cost-effective ways to transport their products through the EU. Reshoring can help to do this by eliminating the red tape.
"Friendshoring" is the act of manufacturing and sourcing from countries that are geopolitical allies, and is gaining considerable interest across the world. Manufacturers are focusing on growing their supplier base in markets that are considered to be stable, dependable and have shared objectives.
Nearshoring is the practice of partnering with suppliers, manufacturers and other necessary entities within a supply chain that is located in countries near the company in question. For instance, a company based in the UK might practice nearshoring by working with a supplier in Ireland rather than China. This can help strengthen the economy by creating manufacturing jobs, reducing unemployment, and balancing trade deficits.
A Make UK survey stated that 2-in-5 businesses are considering a switch to UK manufacturers as rising shipping costs bite into margins and threaten growth. Almost half (45%), said high shipping costs were the biggest challenge to international expansion.
However, it doesn’t always have positive results as some products are best left offshore, particularly those native to other countries.
Eighty-two percent of manufacturers say that supply chain diligence is firmly on their minds in 2023. Why, however, does there seem to be a lag between citing its importance and adopting digital technologies that can help monitor and manage the whole supply chain?
Manufacturers who are not addressing supply chain diligence will find that they increasingly lose out on contracts where they are outbid by smaller, more agile specialists who are focused on bringing in technologies like Industrial Internet of Things (IoT), or robotic process automation (RPA) to enhance their specialisms. Customers will also look to these companies to meet their more specific needs and get better value for their money.
"Cloud deployment is clearly the top technology that is changing how supply chains operate with AI second."
Opportunities to mitigate risk
As the supply chain world becomes more and more uncertain, there are real opportunities for manufacturers to work together with business implementation and technology specialists such as Microsoft Partner, HSO, to help businesses understand the benefits of connecting their supply chains, from improving processes and digitising B2B documents like advanced shipping notices, invoices, and customs documents, , to using AI (Artificial Intelligence), ML (Machine Learning), and data analytics and dashboards to predict future problems and mitigate risk, by taking relevant actions sooner rather than later.
Assessing and understanding what is happening in your supply chain is the first step to knowing how and where to respond.
If you would like to create a hyperconnected supply chain which offers a digital thread throughout your manufacturing business and a real-time, integrated view of product lifecycles, contact HSO to find out how we have already helped other manufacturers and how we can help you.