The Need for Factory 4.0 in Modern Manufacturing
Is It Time to Embrace Factory 4.0?
A Comprehensive Guide for Modern Manufacturing
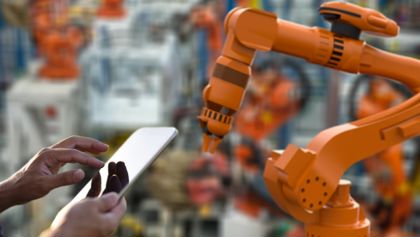
Unlock the Potential
In an era marked by rapid technological advancements and shifting industrial paradigms, the concept of Factory 4.0 has emerged as a beacon of transformation in manufacturing. At HSO, we recognize the critical importance of this evolution and are committed to guiding businesses through this transformative journey. But what exactly is Factory 4.0, and how do you know it's time to integrate it into your operations?
Understanding Factory 4.0
Factory 4.0 represents the next wave of technological advancement in production technologies. Characterized by the integration of digital technologies such as the Internet of Things (IoT), data analytics, and artificial intelligence (AI), Factory 4.0 is not just a trend — it's a fundamental shift in how manufacturing processes are conceptualized and executed. This new era of smart manufacturing is about creating interconnected, intelligent systems that can autonomously monitor, analyze, and optimize industrial processes.
The Shift from Traditional Manufacturing
The transition to Factory 4.0 marks a significant departure from traditional, labor-centric manufacturing practices. In conventional settings, processes are mostly manual, automation is limited, and systems often operate in silos without efficient communication and data sharing. This approach, while functional in the past, is increasingly inadequate in today's fast-paced, innovation-driven market.
- 1
Limited Automation and Manual Processes
In an environment where speed and efficiency are paramount, relying heavily on manual processes can hinder responsiveness and agility.
- 2
Siloed Systems and Lack of Integration
The absence of integrated systems leads to inefficiencies and data bottlenecks, making it challenging to have a unified view of operations.
- 3
Inefficient Utilization of Data
Modern manufacturing generates vast amounts of data. Without the tools to analyze and leverage this data, opportunities for optimization and innovation are lost.
- 4
Outdated Maintenance and Quality Control Methods
Traditional maintenance practices, often managed through spreadsheets or disconnected systems, lack the predictive capabilities essential for minimizing downtime and ensuring quality.
Embracing Factory 4.0 with HSO
Transforming Operations with Smart Technology
We leverage the power of Microsoft’s cutting-edge platforms to integrate IoT, AI, and advanced analytics into manufacturing operations. This integration transforms factories into smart, responsive environments where every component and process is interconnected and optimized for peak performance.
Streamlining with Data and Analytics
Our approach to Factory 4.0 places a strong emphasis on data utilization. By harnessing the power of analytics, we provide manufacturers with insights that drive efficiency, reduce waste, and open new avenues for innovation.
Predictive Maintenance and Quality Control
Transitioning to predictive maintenance models, our solutions enable manufacturers to anticipate and address issues before they escalate. Similarly, advanced quality control methods, powered by real-time data, ensure product excellence and consistency.
The journey to Factory 4.0 is not just an upgrade — it's a fundamental shift towards a more efficient, innovative, and sustainable future in manufacturing. With HSO and Microsoft’s technologies, embracing this future is not just a possibility; it’s a reality within reach. Are you ready to take the next step in your manufacturing evolution? HSO is here to guide you into the era of Factory 4.0, where opportunities for growth and innovation are boundless.
Learn More About
Modernizing Manufacturing Resources