UK businesses have switched on to the power of AI for manufacturing
Using AI in Predictive Maintenance to Minimize Downtime
With downtime costs skyrocketing, artificial intelligence is helping prevent unexpected stoppages and propel predictive maintenance into the mainstream.
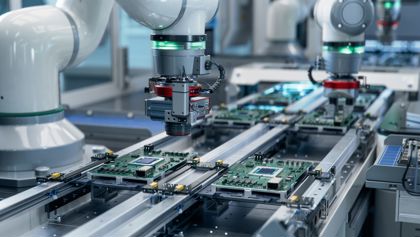
Imagine a world where your maintenance budget isn’t drained by unexpected breakdowns; where engineering teams focus on long-term, strategic improvements rather than continuous fire-fighting. AI-powered predictive maintenance makes this vision a reality.
By foreseeing potential failures with unprecedented accuracy, this exciting advancement has the potential to transform how companies approach maintenance. Indeed, it already is – as shown by the real-world case studies at the bottom of this article.
Skyrocketing Cost of Downtime
Maintaining uptime is one of the most formidable challenges faced by manufacturers. One stopped machine can slam the brakes on an entire production line, posing an immediate threat to delivery schedules and revenue.
Recent research shows that, on average, factories are experiencing 20 unplanned downtime incidents a month. Despite being six fewer than previously recorded, each failure is taking longer to recover from. More alarmingly, the cost of downtime has soared.
Spiralling inflation and production lines running at higher capacity mean that an hour of unplanned downtime costs manufacturers at least 50% more today than five years ago. The financial toll varies, from $39,000 an hour for fast-moving consumer goods (FMCG) facilities, up to $2m in the automotive sector.
The global study also found that heavy industries and large industrial companies face particularly high costs. Fortune 500 manufacturers, for example, are expected to lose almost $1.5 trillion this year to downtime, more than 10% of their revenue.
Manufacturers are having to find a balance between keeping downtime to a minimum while avoiding over-maintenance – i.e. unnecessary machine shutdowns and holding expensive inventories of spares.
Many are turning to predictive maintenance, a strategy proven to reduce downtime by as much as 50%, extend asset lifespan by up to 40%, and improve safety without the drawbacks of over-maintenance.
Traditional vs Predictive Maintenance
Given the financial and reputational costs associated with machine downtime, it’s surprising that two in three manufacturers continue to rely on high-risk run-to-fail or time-based maintenance strategies. These approaches involve fixing equipment only when a failure occurs or following predetermined schedules. Why outdated preventative maintenance methods endure stems from a combination of factors, ranging from predictable costs to the comfort of familiarity.
However, as modern factory assets grow increasingly complex and interconnected, and real-time monitoring becomes standard practice, companies are seeking a more advanced and proactive maintenance method. Such a transition not only mitigates the issue of downtime but also reveals opportunities to optimise machine performance that were previously overlooked or hidden.
Predictive maintenance works by using data to anticipate potential failures before they disrupt operations. Unlike reactive or scheduled maintenance, predictive maintenance relies on real-time monitoring, sensors, and data analytics to assess the condition of machinery.
In embracing this approach, manufacturers can move from a ‘fix-it-when-it-breaks’ mentality to strategic, data-driven maintenance planning. Doing so offers clear advantages that go beyond traditional maintenance practices.
By forecasting and preventing equipment failures, manufacturers minimise downtime and increase operational efficiency. The ability to address issues before they escalate saves costs by reducing the need for emergency repairs and extending the lifespan of machinery. Additionally, improved machine reliability ensures a consistent production output, enhancing overall factory performance.
The roots of predictive maintenance reach back to the early days of condition-based monitoring when engineers began exploring how to use data to foresee equipment failures. Advancements in computer power, sensor technology and connectivity have moved predictive maintenance from an idea to a practical and essential strategy.
The recent emergence of AI in manufacturing has brought about transformative changes in predictive maintenance, significantly enhancing its capabilities.
39%
of British firms have already incorporated AI into their daily operations (Amazon)
55%
of UK manufacturers already use, or are planning to implement, AI and Machine Learning (Make UK)
43%
more likely to see higher revenue, profitability and competitiveness among engineering firms who use AI (Forrester)
How AI in Predictive Maintenance Takes Manufacturing to New Heights
The integration of AI into predictive maintenance brings an unparalleled level of sophistication and effectiveness, significantly boosting its impact. This can be seen across four key aspects:
- Enhanced Data Processing and Decision-Making
- Advanced Pattern Recognition
- Scalability and Adaptability
- Sustainability Goals
1. Enhanced Data Processing and Decision-Making
AI excels at processing vast amounts of data quickly and accurately. In predictive maintenance, AI algorithms analyse complex data sets from various sensors and sources alongside historical data to provide more nuanced insights into equipment conditions.
The fact that machine learning models can adapt and learn creates a dynamic feedback loop, enabling algorithms to continually refine their forecasts and help companies stay ahead of maintenance issues. The result is faster, more accurate predictions of potential failures and a reduced likelihood of false alarms.
The speed of AI is as impressive as its accuracy. When an intervention is required, information can be swiftly relayed to the maintenance team and supervisors, prompting immediate action and ensuring machines are back up and running with minimal delay.
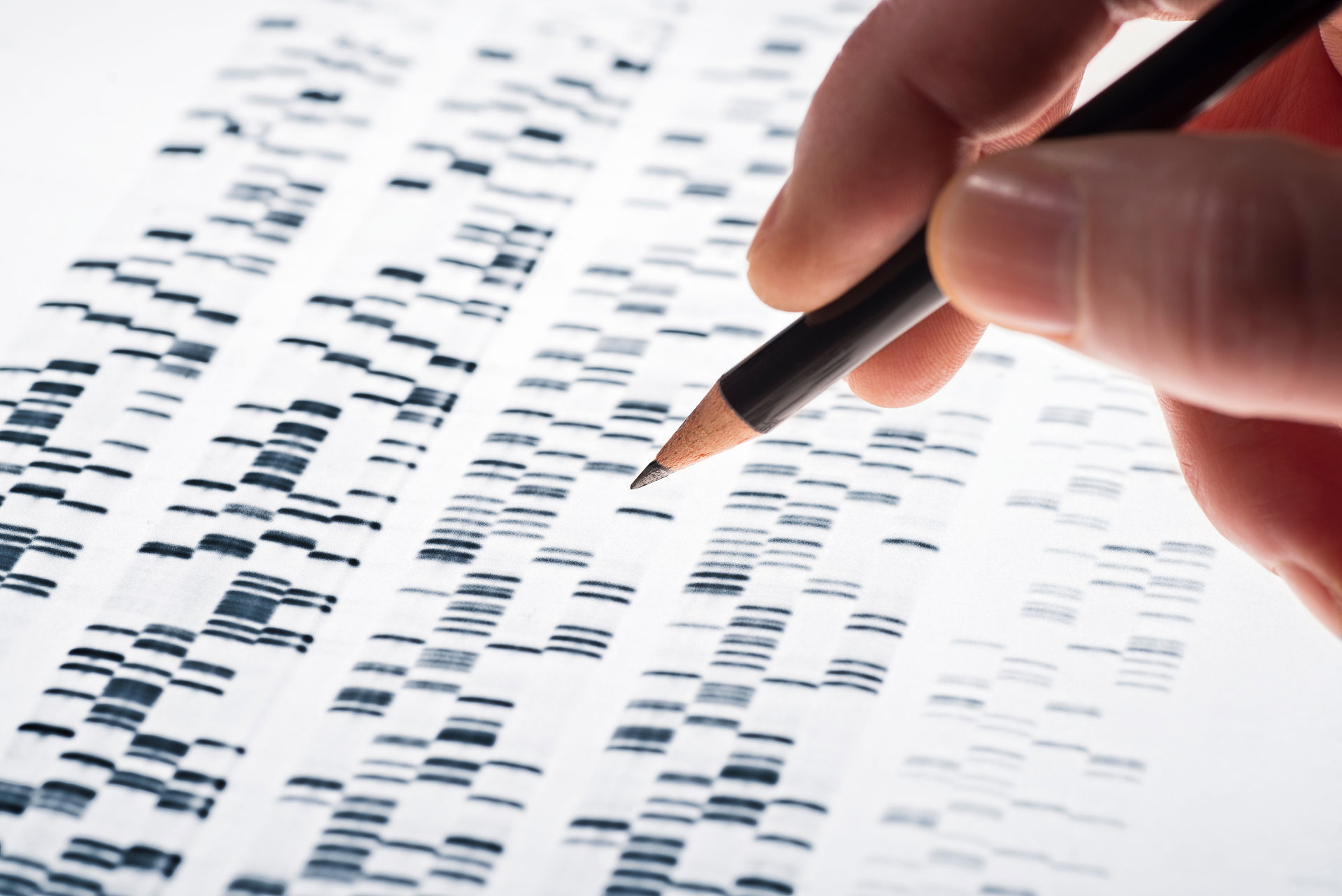
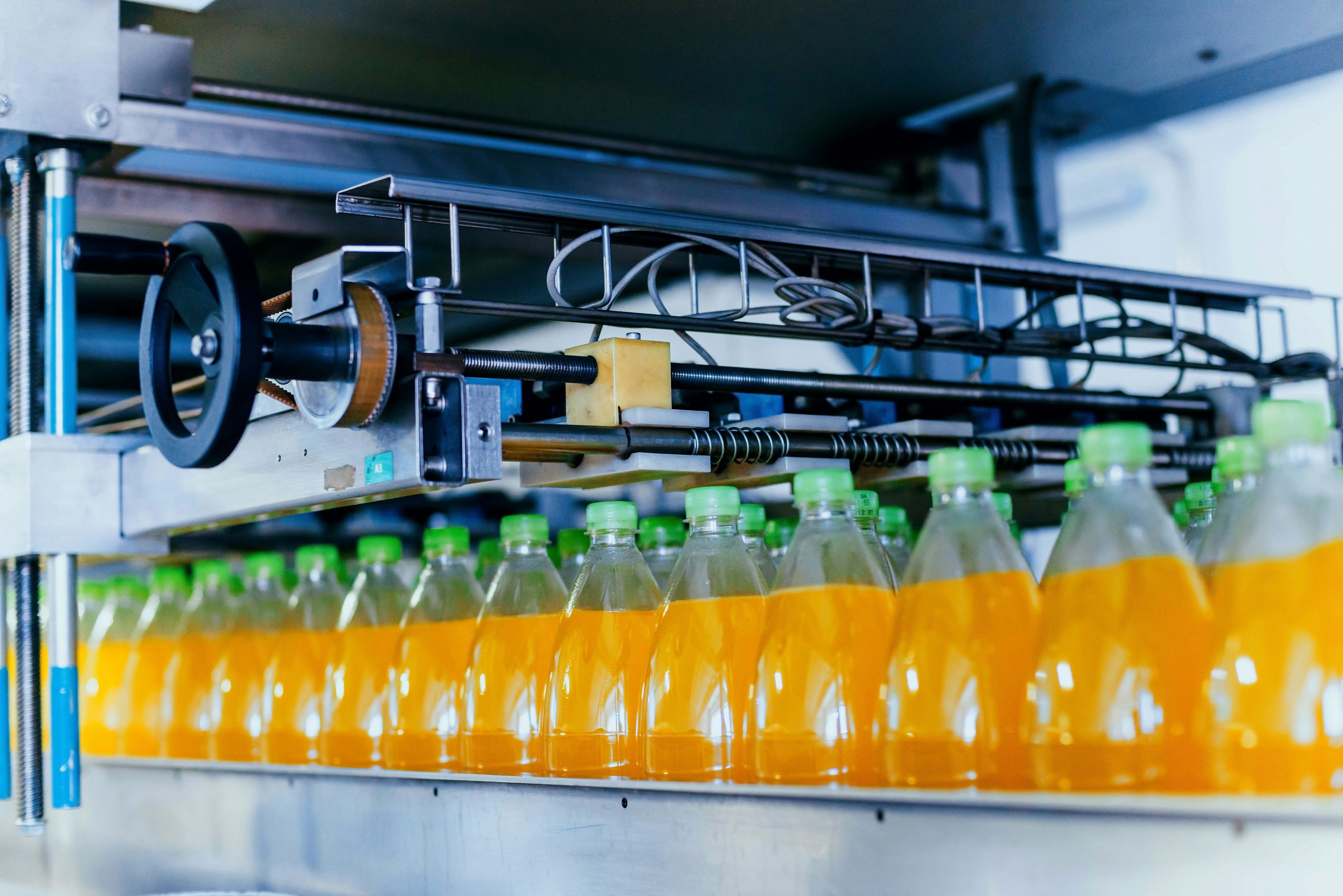
2. Advanced Pattern Recognition
AI algorithms, particularly those based on machine learning, surpass all other methods for pattern recognition. They can identify subtle correlations and anomalies in machine data that may go unnoticed by traditional analytics and humans alike. This heightened sensitivity helps detect early signs of equipment degradation or failure.
Additionally, AI algorithms can optimise maintenance schedules based on equipment health and performance trends. Prioritising maintenance tasks according to the likelihood and severity of potential failures enables manufacturers to allocate resources more efficiently and effectively.
3. Scalability and Adaptability
Factories often house a mix of machinery with different specifications, operational requirements and ‘intelligence’ levels. The adaptability of AI allows predictive maintenance strategies to scale with the needs of an operation, accommodating the complexities of various equipment types and configurations. This will prove crucial as companies increasingly pivot from low-cost, high-quantity to a more flexible and varied manufacturing setup.
Scalability also extends beyond the confines of a single facility. An AI-driven predictive maintenance system can be deployed across multiple locations, allowing those with a globe-spanning manufacturing network to implement a standardised and efficient strategy.
The potential for a worldwide data repository further boosts scalability. By centralising data from various machines and factories, manufacturers can create a shared knowledge pool that enhances AI learning.
When a system in one location discovers new insights or the best way to approach specific issues, the whole organisation benefits from that knowledge, fostering continuous improvement and efficiency across a global footprint. This positive impact can be spread even wider by sharing such insights with suppliers and customers.
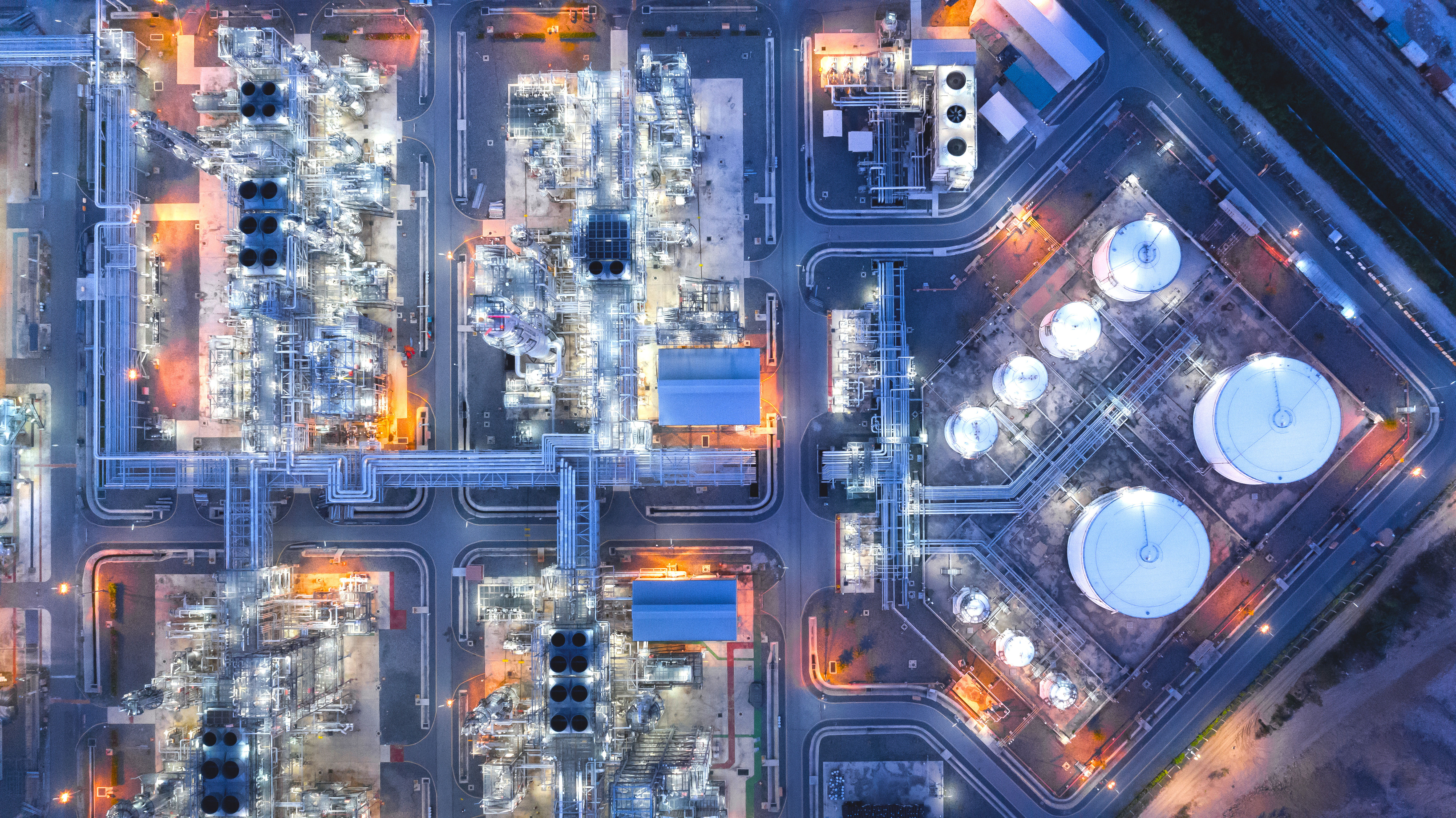
4. Sustainability Goals
AI in manufacturing plays a pivotal role in helping companies meet their environmental commitments. By identifying and rectifying inefficiencies in equipment, AI-driven predictive maintenance optimises machinery and delivers significant energy savings.
Machines operating at peak efficiency need replacing less frequently, reducing the environmental impact of manufacturing and disposing of old machinery. Equally, it helps conserve materials and resources by avoiding unnecessary maintenance activities.
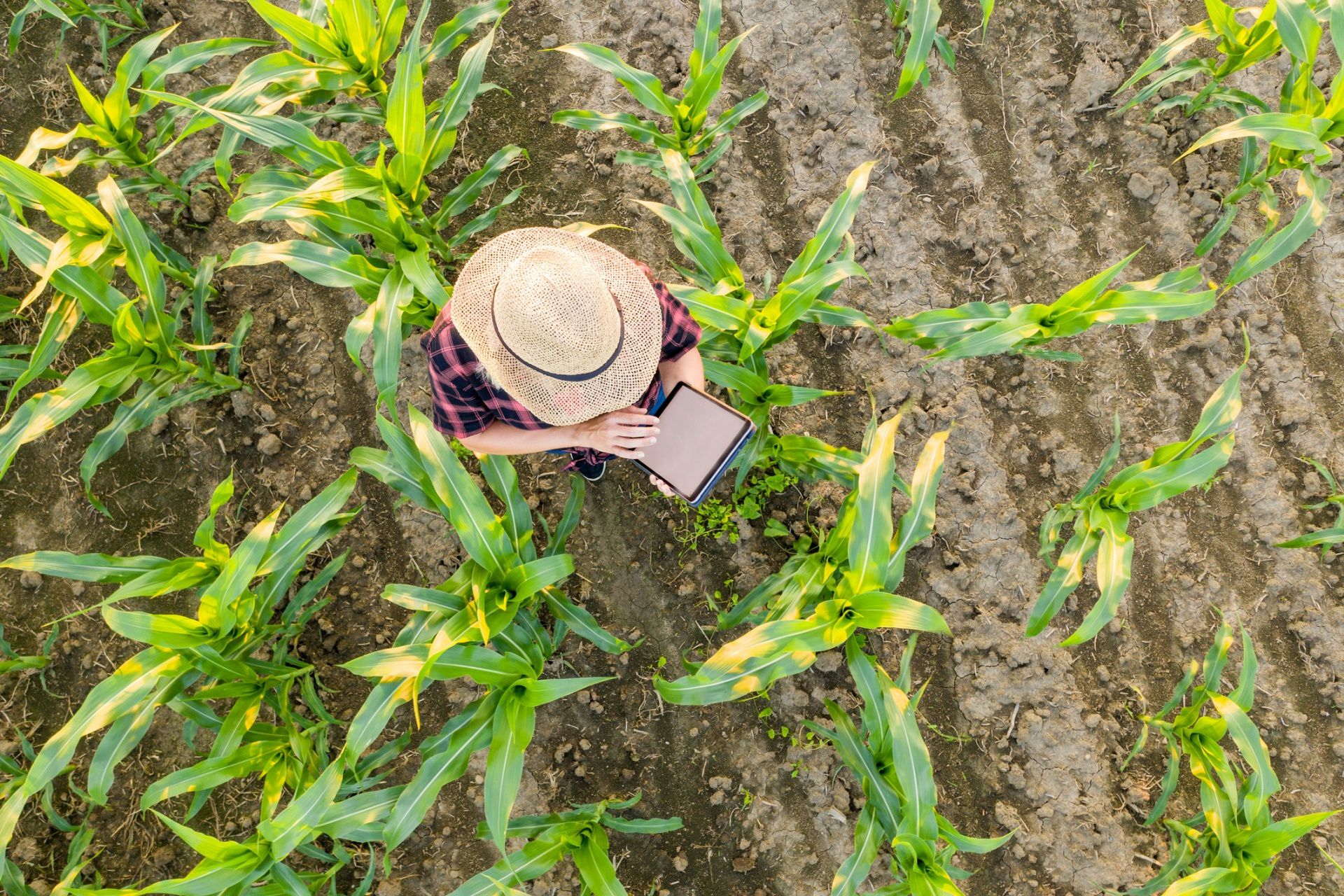
Three Real-World Examples of AI in Maintenance Making Tasks Smarter and Easier
1. Toyota
Toyota is no stranger to AI in manufacturing. For almost a decade, the automotive powerhouse has been using AI within its organisation and products. Vehicle maintenance has been a key focus of AI-driven enhancements.
Connected vehicles have hundreds of sensors. Toyota engineers have been using data from consenting vehicles to build machine learning models for the most common maintenance items, including batteries, brakes, tyres and oil. Dozens of other components are currently being investigated.
Toyota says this suite of predictive models will help make customers aware of potential maintenance issues before the driver feels or hears changes in performance, such as with brake pads and rotors.
2. Caterpillar
With 1.4 million connected assets – machines and power systems – in the field, Caterpillar generates a huge amount of data every day. An advantage to collecting and analysing all this data is that it allows CAT dealers to monitor the condition of equipment, detect possible issues and alert customers to take action before failure strikes.
Data from more than 20 different sources per asset, from equipment sensors and inspection records to fluid analysis, is analysed to give CAT dealers an accurate picture of performance and health so they can recommend to customers what parts and services are needed and when.
3. BASF
BASF began its journey to an AI-powered future 10 years ago by exploring the possibilities and benefits of machine learning models. Today, the largest chemical producer in the world has developed and applied AI in all areas of its day-to-day business, from production and engineering to R&D and management.
One such initiative involves an electrical substation that powers BASF’s production plant in Beaumont, Texas. Condition-based monitoring evaluates live data across more than 100 variables from critical connected assets within the substation, generating proactive recommendations to minimise failure and optimise maintenance strategies.
Read our four blogs from the
Manufacturing AI series